Japanese company Rapidus and IBM announced on December 13th of this year that they have established a cooperative relationship to mass-produce 2-nanometer logic semiconductors.
IBM has been actively engaged in the research and development of cutting-edge semiconductors for many years and once had its own 300-millimeter wafer factory in New York State, USA (which was transferred to Global Foundries in 2014, and later, the factory was acquired by ON Semiconductor). In addition, IBM has been producing semiconductors required for its own brand of computers, while also providing customers with cutting-edge process technology research and development services and wafer foundry services.
IBM's cutting-edge process technology R&D services, as a Common Platform, have effectively reduced R&D costs and ensured the resources of a second supplier by creating universal process technologies and production lines. Initially, IBM, Chartered Semiconductor Manufacturing (now Global Foundries), and Samsung Electronics provided universal R&D processes in their respective factories to develop 90-nanometer processes (and more advanced ones). Later, Infineon and Freescale Semiconductor (now NXP Semiconductors) also participated in the development of 32-nanometer processes. In addition, IBM collaborated with Sony and Toshiba to develop and produce the "Cell" used for PLAYSTATION 3, and later, it partnered with AMD to develop SOI-related technologies. Last year (2021), it was reported that Intel was conducting R&D with IBM in the field of cutting-edge semiconductors. In summary, IBM has had cooperative experience with most semiconductor manufacturers.
Advertisement
Research and development and mass production are completely "two different things."
In terms of the previous Common Platform, it was actually a "precise copy" (Copy Exactly), which means completely replicating the process built on IBM's production line and applying it to other "partner factories." As a result, a very high yield rate was achieved from the initial stage.
However, according to my understanding, even with the same equipment, the same process, and the same equipment parameters, the same yield rate may not be achieved. When IBM, Toshiba, and Sony were producing Cell processors in their respective semiconductor factories, it is said that only IBM had the lowest yield rate. It can only be said that Japan was still producing cutting-edge logic semiconductors at the time, so it had mastered the corresponding mass production technology.
As mentioned above, after 2014, IBM began to gradually give up the mass production line, and the company only retained the R&D team for cutting-edge processes. We can see a glimpse of this from the remarks of Mr. Dario Gil, Senior Vice President and Director of IBM Research, when he was interviewed by journalists: "The development trend of semiconductors is innovation, which can only be achieved through research and development." The process miniaturization that has supported Moore's Law to this day is that only finer processes can help accommodate more transistors, and the performance of a single chip is also richer. Ultimately, the added value of the end product is also higher, which has become the source of corporate performance growth. In recent years, companies such as Google and Microsoft have been competing to design LSI/SOC on their own, that is, designing and producing dedicated LSIs according to their own needs, and then providing customers with special services. This approach is the consistent "approach" of Japan's OA (Office Automation, office automation) equipment companies, which has not changed for many years.
Why does Rapidus want to introduce IBM's 2-nanometer process?
After establishing a cooperative relationship, Rapidus will send technical personnel to learn at IBM's "Albany Nano Tech Complex" located in Albany, New York State, USA (where IBM mainly promotes R&D work). At the same time, Rapidus is also cooperating with companies other than IBM to develop a 2-nanometer process, with the goal of starting mass production in the second half of the 2020s (between 2026 and 2029).
Rapidus is actively building a system for developing cutting-edge semiconductors, and like IBM, it has established a partnership with imec (a European research center specializing in the development of cutting-edge semiconductor processes).However, it is concerning whether the 2-nanometer process can be smoothly introduced in the latter half of the 2020s. Since it is a mass production project that starts from scratch and does not follow the miniaturization route step by step, it objectively requires a certain amount of time. The cooperation between IBM and Rapidus is a direct transition from Planar to FinFET type. Even if it directly challenges the GAA type, it is also very difficult (let alone that Rapidus has avoided the GAA type this time). In this regard, Mr. Jun Yoshikawa, the representative director and president of Rapidus, said: "The transition from FinFET to Nano-sheet (nanosheet) is a huge leap. Without long-term experience in cutting-edge process development, it is difficult to grasp the essence of GAA technology. Due to structural changes, learning in Albany will be beneficial for the leap."
At the same time, at the press conference, Mr. Yoshikawa also pointed out: "Although it is a big challenge, it is not insurmountable." Although GAA can adopt most of the processes of FinFET, it is also difficult to learn. In addition, according to the "nanometer process technology roadmap" publicized by the logic semiconductor manufacturers in the 2022 International Roadmap for Devices and Systems (IRDS), the mass production of the 2-nanometer process will be in 2025. The 1.5-nanometer process will be mass-produced in 2028, and the 1.0-nanometer process will be mass-produced in 2031. Even if Rapidus and IBM successfully mass-produce the 2-nanometer process in the latter half of the 2020s (from 2026 to 2029), their process may still be 1 to 2 generations behind other advanced manufacturers.
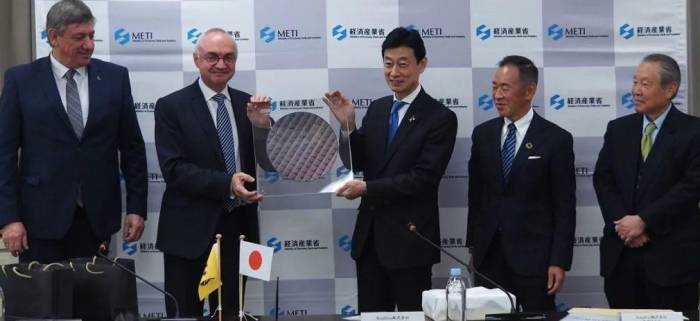
At the SEAJ booth of SEMICON Japan 2022, a transistor shape model was exhibited.
On the other hand, it can be seen that IBM mainly has the following two purposes:
First, to find and secure corporate partners for collaborative research and development of cutting-edge processes;
Second, to increase a foundry company that can actually produce and manufacture wafers.
It is well known that IBM does not have a foundry factory, and Samsung Electronics has been a contract manufacturer for IBM's cutting-edge logic semiconductors for a long time. According to foreign media reports, the yield of the most advanced 3-nanometer process is very low and difficult to improve (in addition, there are also reports that the yield of 5 nanometers has only recently reached 70%). The above information may be hearsay, but it is said that TSMC also put in a lot of effort in the mass production of 3 nanometers. Therefore, it takes a long time to mass-produce cutting-edge processes and ensure a high yield. For IBM, finding a foundry production manufacturer other than Samsung Electronics is very important.
In fact, at the opening ceremony (i.e., discussion meeting) of SEMICON Japan 2022, Mr. Yoshikawa pointed out: "Japan is 10 to 20 years behind in cutting-edge logic semiconductors. If it can obtain technical support from IBM, it will be very beneficial." At the press conference on December 13, 2022, Mr. Tetsuro Higashi, the chairman of the board of Rapidus, said: "IBM proposed such a Japan-US cooperation project two years ago."In this sense, Rapidus is eager to quickly master the cutting-edge process technology, and IBM is looking for a second foundry manufacturer, which can be described as a "perfect match" between the two!
The biggest problem with mass production: Procurement of EUV lithography machines, technology maturity
Even if Rapidus learns IBM's 2-nanometer process technology in Albany, it may not be able to directly mass-produce.
The biggest problem is not IBM, but the EUV exposure equipment installed at SUNY Polytechnic Institute (including Albany Nano Tech Complex): ADT (Alpha Demo Tool, the first generation of EUV prototype equipment), and the third-generation "NEX:3300B". (At least IBM has not announced the introduction of any other new EUV exposure equipment beyond the above two models)
On the other hand, it is necessary to be proficient in using the world's latest EUV equipment in order to mass-produce 2-nanometer processes (and more advanced processes), and to achieve Mr. Kobayashi's claim of "becoming the company with the shortest delivery time in the world."
In addition, it is predicted that TSMC will not use the new generation of high-NA EUV (here, NA=0.55). If there is a technological gap between the EUV available to IBM and the actual mass production required, it is necessary to bridge this gap.
On the other hand, imec, as the world's most advanced cutting-edge technology research and development unit, has also established a cooperative relationship with Rapidus. It is said that imec has also established a cooperative relationship with ASML and is introducing ASML's latest EUV exposure machine for research and development work. Rapidus should be able to use its cooperative relationship with imec to obtain the latest generation of lithography machine technology from ASML and bridge the above gap.
However, another issue is whether Rapidus can obtain the lithography machine. ASML's lithography machine shipment forecast for 2022 is 55 units. In 2023, it is more than 60 units, and the plan for 2025 is 90 units. Although ASML is gradually increasing its production capacity, with the development of semiconductor process miniaturization, the number of layers using EUV will also increase, so in the future, various semiconductor manufacturers will continue to "compete" for lithography machines. It is said that due to the difficulty in purchasing lithography machines, the leader of Samsung Electronics went to ASML for negotiations in the fall of 2020 and successfully introduced 15 units in 2021.
With the start of the company, the Japanese government allocated 70 billion yen (about 3.5 billion yuan) from the national treasury to support Rapidus. It is said that this fund is planned to be used for the company's basic operations, but in fact, the fund will be implemented after a period of time. Even if mass production is achieved, a certain number of lithography machines are needed. In this sense, considering the schedule for building factories and introducing equipment, whether mass production can be achieved in the second half of 2020 is still an unknown.
What will be produced using the 2-nanometer process?After Rapidus disclosed its goal of mass-producing 2-nanometer technology, many voices questioned: "What will be produced with the 2-nanometer process?"
Companies such as Toyota Motor Corporation, Denso, Nippon Telegraph and Telephone (NTT), and IBM have all invested in Rapidus, presumably hoping that Rapidus can manufacture semiconductors on their behalf. However, what is more important now is whether Rapidus can secure cutting-edge fabless customers such as Apple, Qualcomm, AMD, Nvidia, and MediaTek. The aforementioned customers are currently commissioning TSMC and Samsung Electronics to produce semiconductors. These customers, who require advanced processes, fully understand the added value of cutting-edge processes, and even in the 2-nanometer era, there will not be much change.
Here is a discussion topic similar to process miniaturization: What to store after increasing storage capacity? Each time, new applications for NAND (occasionally accompanied by price drops) emerge. There is a need to process the massive amount of data that will be generated in the future with higher speed and lower power consumption. In addition, the performance required by supercomputers is still unclear. With improved computing power, real-time AI processing has been achieved, and complex, long-duration molecular motion can be simulated. From historical experience, some company will definitely find a new use for it and establish a new business opportunity and market. Even with 2-nanometer technology, it will follow the above rules. Therefore, it is important to master the semiconductor performance technology required by user companies.
Moreover, to create the aforementioned new market, it is not only necessary to cultivate fabless semiconductor manufacturers but also to improve the industry's design and research and development environment. In the past IDM (Integrated Design and Manufacture, vertical integration manufacturing) model, a company designed and produced semiconductors, and the wafer factory only needed to produce semiconductors for the parent company, and it was very clear what kind of semiconductors were needed. However, in today's era where the division of labor between foundries and fabless companies is very clear, having only production capacity is meaningless. It is more important to provide products with higher value to customers based on their own capabilities. Even with high technology, if there is no customer recognition, transactions cannot be generated.
Regarding Rapidus's business, Mr. Koike listed three points: First, talent cultivation; second, building a production system based on the end market and products; third, achieving green transformation (GX) based on semiconductors. It is indeed very difficult to start developing cutting-edge semiconductors now and catch up with advanced manufacturers within a certain period of time. Mr. Koike, who has been active in the semiconductor industry for many years, and Mr. Toshio, should fully recognize this point. Mr. Koike has accumulated production experience since the era of Trecenti Technology (a foundry factory established by Hitachi and UMC, now the N3 production line of Renesas Electronics's Nikko factory), and still has a high enthusiasm for foundry construction. In this sense, Rapidus is expected to develop mass production processes and overcome the above difficulties under the leadership of Mr. Koike. Can cutting-edge logic semiconductors really be produced again on Japanese soil? Let's continue to pay attention to the future trends of Rapidus, which has taken the first step towards achieving this goal.
Post Comment