Entering the post-Moore era, the ability to integrate technologies is increasingly tested for chip manufacturers. Chips must continue to evolve towards miniaturization, multi-pins, and high integration. In addition to the conventional process of miniaturization, various advanced packaging technologies have become indispensable. As the best way to enhance chip performance in the post-Moore era, advanced packaging technology platforms represented by flip-chip have become the preferred packaging solution for medium and high-performance products. Among flip-chip technologies, FCBGA technology is the mainstream.
Apple is a loyal adopter of FCBGA packaging technology. Apple first applied FCBGA packaging technology in its own processor in 2006, on the A5 processor, which was used in the first-generation iPad and iPhone 4S. Since then, Apple has been using FCBGA packaging technology and continuously improving and enhancing its performance, up to the recently launched PC processor M series. Recently, Apple's supplier LG Innotek has started to enter the FCBGA substrate market, and the industry speculates that it may provide FCBGA substrates for Apple's M series chips, which also reflects the market demand for FCBGA from the side. The packaging technology used by Apple is flourishing.
Advertisement
FCBGA technology is blooming in various fields.
FCBGA (Flip Chip Ball Grid Array, which means "flip-chip ball grid array packaging") is a packaging technology. This packaging method inverts the chip and connects it to the packaging substrate, and then uses spherical solder points to fix the packaging to the substrate. FCBGA first appeared in the early 1990s. In 1997, Intel first applied FCBGA packaging technology to processors, which is an important milestone in the history of FCBGA technology.
In 1999, Intel launched the first chip using FCBGA packaging technology, the Pentium III 500 processor. Before that, the packaging method of processors was mainly multi-chip modules (MCM), which integrated multiple chip components in a package. Due to the complex connection lines, the MCM packaging method had problems such as signal interference and poor thermal management. In contrast, FCBGA packaging technology flips the chip over and connects the metal bumps on the back of the chip to the metal balls printed on the packaging. This packaging method can achieve higher chip density and smaller packaging volume, thereby greatly improving integration and system performance. The launch of the Pentium III 500 processor marked the commercial application of FCBGA technology, which became one of the hot topics in the electronics industry at that time.
As FCBGA technology gradually improved, manufacturers continuously enhanced its reliability, especially in terms of solder joint connections, micro-adjustments, and casing packaging. The advantages of FCBGA packaging technology mainly include:
Higher density: Because FCBGA packaging technology can install more chip pins within the same packaging area, achieving higher integration and smaller packaging size.
Better thermal performance: FCBGA allows the chip to be directly connected to a heat sink or heat dissipation plate, thereby improving the efficiency of heat transfer.
Higher reliability and electrical performance: Because it can reduce factors such as resistance and capacitance between the chip and the substrate, it improves the stability and reliability of signal transmission, and also improves the speed and accuracy of signal transmission.In summary, the FCBGA (Flip Chip Ball Grid Array) packaging technology offers numerous advantages, such as high integration, small size, high performance, and low power consumption. FCBGA is suitable for a variety of chips and is commonly used for high-performance chips such as CPUs, microcontrollers, and GPUs. It is also applicable to network chips, communication chips, storage chips, digital signal processors (DSPs), sensors, audio processors, and more. FCBGA is currently an ideal packaging technology for mobile devices and is widely used in smartphones, tablets, and other mobile devices.
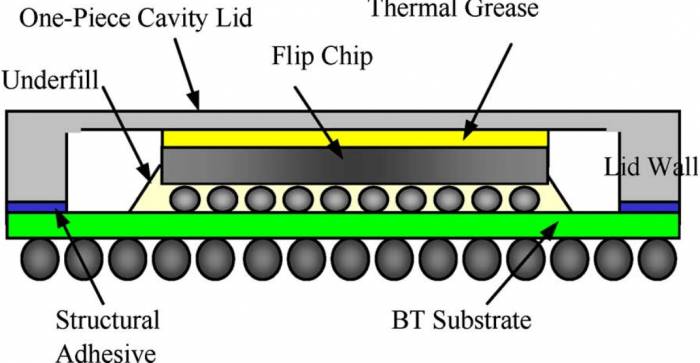
It is these advantages that have made FCBGA one of the mainstream technologies in modern semiconductor packaging. Many large semiconductor companies and electronic product manufacturers, such as Intel, AMD, NVIDIA, Qualcomm, Apple, and Samsung, are using FCBGA technology.
As one of the pioneers of FCBGA technology, Intel Corporation commonly uses this packaging technology. Today, Intel's Core and Xeon series processors, chipsets, memory chips, and wireless network cards, among other electronic components, all employ different types of FCBGA packaging technology. For example, the Core i9-11900K processor uses FCBGA1700 packaging, the Intel Z590 chipset uses FCBGA1492 packaging, Optane memory modules use FCBGA1440 packaging, and the Intel AX210 wireless network card uses FCBGA946 packaging. AMD's Athlon XP processors also utilize FCBGA packaging technology.
It is worth mentioning that FCBGA technology is also used in 3D packaging. The high-density and high-reliability characteristics of FCBGA technology make it highly suitable for chip packaging in 3D packaging. In 3D packaging, the top-layer chip and the bottom-layer chip need to communicate through fine electrical connections, known as TSV (Through Silicon Via). FCBGA technology can encapsulate the top-layer and bottom-layer chips on either side of the TSV, thereby achieving electrical connection between them.
In Yole's statistical data on advanced packaging technologies, FCBGA is one of the most profitable niche packaging markets, followed by 2.5D/3D packaging, FCCSP, and so on. As an important chip packaging technology, the market demand for FCBGA is also growing rapidly with the rapid development of technologies such as mobile devices, smart homes, and the Internet of Things. According to data from market research institutions, the global FCBGA packaging technology market is expected to continue to grow rapidly in the coming years, with the market size expected to exceed 20 billion US dollars by 2026. More and more companies and research institutions are investing in the research and development of FCBGA packaging technology, continuously driving innovation and upgrades in FCBGA packaging technology.
Who are the main players in the FCBGA market?
The development of FCBGA technology is the result of the collaborative efforts of multiple manufacturers, who have made contributions in areas such as packaging technology, connection technology, and thermal management technology. Next, let's mainly talk about the players in the two major areas of packaging technology and substrates in the FCBGA market.
In the FCBGA packaging field, in addition to IDM manufacturers such as Intel, Infineon, Micron, and NXP, who have conducted a lot of research and development work in this field, there are also third-party technology providers such as ASE, Jiangsu Chang'an, and Amkor. Among them, ASE has developed a variety of FCBGA packaging technologies, including CSP (Chip Scale Package) and FPBGA (Fine-Pitch Ball Grid Array); Amkor also has a variety of FCBGA packaging technologies, including FCBGA and TFBGA (Thin Fine-Pitch Ball Grid Array).
In recent years, the rise of domestic manufacturers in the fields of CPUs, GPUs, and other high-performance chips has increased the demand for FCBGA packaging technology. In response to market demand, some domestic suppliers with strong technical capabilities and rapid business growth have emerged, such as Moore Elite. It is reported that Moore Elite's Wuxi SiP Advanced Packaging Test Center can provide a complete solution for Flip-Chip packaging of products such as DPU, HPC, CPU, GPU, high-end servers, high-performance ASSP, and FPGA, including packaging design, simulation, engineering batches, and mass production, with an FCBGA capacity of up to 1KK per month. In addition to FCBGA, Moore Elite can also provide various packaging types such as SiP, QFN, WB, and FCCSP. Its SiP team has more than 15 years of packaging technology and engineering experience, having completed SiP development work for international large factory customers, which also brings more choices for small and medium-sized chip companies.The substrate is also an important support for FCBGA packaging technology. Common substrate materials used in FCBGA include printed circuit boards (PCBs), silicon substrates, and copper substrates. The specific material used depends on the application requirements and cost considerations.
In FCBGA packaging, the commonly used carrier material is ABF (Advanced Build-up Film) carrier, which is a multi-layer PCB. For most applications, ABF carrier is a cost-effective choice that can meet most packaging requirements. The characteristics of ABF carrier are that it is very thin, light, and flexible, with good thermal conductivity and low dielectric loss, making it one of the ideal carrier materials for FCBGA packaging technology. The quality and design of the ABF carrier throughout the packaging process are crucial to ensuring the quality and reliability of FCBGA packaging.
The other two mentioned above are relatively more expensive. Silicon substrates can provide high electrical performance and lower signal latency, but they are relatively more expensive; copper substrates are a special type of PCB that uses copper foil instead of standard conductive materials. Copper substrates can provide better thermal conductivity and are suitable for applications that require high power processing.
The main global substrate suppliers include Toppan Printing and Ibiden in the Japanese region, Unimicro and Nanya in the Taiwan region, LG Innotek in South Korea, and AT&S and Suzhou Qun Ce in the domestic region. With the increasing demand for high-performance chips driven by 5G and AI applications, global leading companies are actively expanding production capacity.
For example, in 2022, Samsung's subsidiary Samsung Electro-Mechanics has spent about 2 trillion won on the expansion of FCBGA facilities. Samsung Electro-Mechanics estimates that the FCBGA substrate market will grow at an annual rate of 14% over the next five years, reaching 17 billion US dollars by 2026. "The semiconductor packaging substrate market is smaller than the chip foundry business, but its growth potential is much greater," said Ahn Jung-hoon, the head of the packaging support team at Samsung Electro-Mechanics.
LG Innotek of South Korea announced on February 22, 2022, that the company has decided to invest 41.3 billion won in the "flip-chip ball grid array (FCBGA)" production line, which is LG Innotek's first investment in the FC-BGA business. LG Innotek has been leading the communication packaging substrate market in 5G millimeter wave packaging antennas (AiP) and radio frequency system-level packaging (RF-SiP). The company has acquired substrate technology through years of AiP and SiP product development experience and plans to apply these technologies to the FCBGA business as well.
In addition to commercial manufacturers, there are also a large number of scientists, engineers, technical experts, etc., whose continuous efforts and innovative spirit have enabled the continuous development and improvement of FCBGA technology, turning FCBGA packaging technology from the initial concept into one of the widely used technologies in various electronic products today.
Conclusion
In summary, FCBGA technology has experienced rapid development over the past few decades and has become one of the main packaging methods for core electronic components such as processors, memory, and graphics processors. FCBGA technology will also face higher performance and application requirements in the future, especially in the development of fields such as 5G communication, artificial intelligence, and virtual reality, where FCBGA packaging technology is playing an increasingly important role.
Post Comment