Starting in the second half of 2022, pressure gradually transmitted from downstream to the semiconductor foundry industry. Faced with inventory pressure, IC design companies began to cut orders at the risk of breach of contract, and the utilization rate of various foundries began to show signs of loosening.
A few months ago, the industry was still talking about price increases, shortages, and expansion. In the blink of an eye, price reductions, order cuts, production cuts, and even salary cuts and layoffs have become key words in the industry.
The intensity of news in the foundry market has never been as "dazzling as the chaotic flowers" as it is now. Whether it is TSMC's plan to build a new 3nm factory in the United States, Samsung's increased outsourcing capacity, Intel's claim to compete for the second place in the foundry industry, the foundry industry's chill may not have reached the bottom, or industry giants cutting capital expenditures, all are showing that the foundry industry is facing the era's proposition of increased cyclicality and uncertainty in semiconductors. Foundry giants are also integrating responses at the strategic or tactical level.
Advertisement
On the other hand, driven by Moore's Law, foundries have been closely following advanced processes. In the final sprint of this competition, only TSMC, Samsung, and Intel are left, engaging in a fierce battle at the advanced process nodes.
At present, with market fluctuations, what kind of ups and downs are various foundries facing? What kind of adjustments will the capacity pattern undergo in the future? After the reversal of the supply and demand relationship, how will the foundry market change? In this counterattack and defense battle of the foundry industry, the three giants of foundry are making frequent moves.
Intel: A Long Journey of Transformation
Intel's transformation has been going on for many years.
From the difficult mass production from 14nm to 10nm, Intel is well aware of its lag in process technology and the brand image of "toothpaste factory". Everyone also understands that Intel needs a transformation.
Launching the IDM 2.0 Strategy
At the beginning of 2021, this long journey of transformation ushered in a major turning point - Pat Gelsinger, a veteran of the semiconductor industry who once served as Intel's CTO, was appointed as Intel's CEO.Shortly after taking office, Pat Gelsinger announced the "IDM 2.0" strategy, in which Intel opens up its own foundry services and expands the use of third-party foundry capacity.
Intel has always been an IDM model, covering the entire process from chip design to production to sales, and most of the products are also manufactured in its own factories. Under the IDM 2.0 model, Intel will not only entrust external chip foundries to produce its own chips, such as booking TSMC's 3nm capacity; at the same time, Intel will also develop its own chip foundry business, establishing Intel Foundry Services (IFS) business, and re-entering the chip foundry industry.
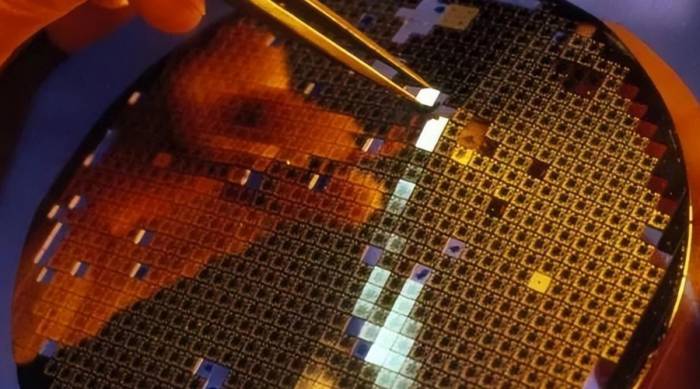
Intel's logic is that IFS will become stronger and better in the process of serving chip customers, and as IFS becomes more advanced in chip manufacturing, the produced chip products will also be more competitive, including chips manufactured internally, which in turn ensures that IFS will not be limited by external foundry capacity, thus forming a positive cycle. In Gelsinger's words in an interview: "IDM makes IFS better, IFS makes IDM better."
However, the contradiction is also obvious. Intel wants to produce chips for itself and also seeks to provide chip foundry services for competitors in other chip fields, such as AMD and Nvidia; similarly, Intel wants to catch up with TSMC and Samsung in the chip foundry business, but it also wants to entrust its best chip products to its competitors for production, which is equivalent to reducing its own chip manufacturing scale while also giving part of the profits to TSMC and other competitors.
However, Intel has indeed found the fulcrum to leverage the IDM 2.0 plan, that is, TSMC and Samsung cannot meet the needs of all customers. Or, under the current market environment, a diversified foundry strategy has become the choice of many chip design manufacturers.
In March of this year, Nvidia CEO Huang Renxun said: "Intel is willing to let us use their manufacturing plants, and we are also very interested in exploring this possibility."
In July, before Nvidia made a move, Intel took the lead in announcing that it would foundry chips for MediaTek. MediaTek said that we have always adopted a multi-source strategy, in addition to maintaining close cooperation with TSMC on advanced process nodes, this cooperation will strengthen our supply of mature process nodes.
In addition, Apple's core chip production is also mainly foundry by TSMC, but Apple CEO Cook recently said that he wants to purchase chips from the United States.
Although TSMC is the absolute leader in the chip foundry field, holding more say, Intel's entry has truly brought new choices for chip companies. In July last year, Intel announced that it would produce chips for Qualcomm, and Amazon has also become a customer of its foundry business.At the same time, subsidies will accelerate the pace of factory construction, which will be a positive signal for Intel's foundry business, gradually competing with TSMC and Samsung head-on with advanced processes.
In August of this year, the "Chips Act" enacted by the United States prompted Intel to initiate its factory construction plan in the U.S.; in addition, the European Union also put forward the "European Chips Act" with 43 billion euros to support the European chip industry, and Intel announced that it will invest in the construction of six major chip-making bases in Europe, with a plan to invest 80 billion euros over ten years.
IDM 2.0 Strategic Transformation
At the Intel On Technology Innovation Summit held in September this year, Gelsinger said that Intel's foundry services will usher in the "era of system-level foundry", which is different from the traditional foundry model of only supplying wafers to customers. Intel provides wafer manufacturing, packaging, software, and chiplets.
Wafer manufacturing: Provides customers with its process technology, such as innovative technologies such as RibbonFET transistors and PowerVia power supply technology.
Packaging: Provides customers with advanced packaging technology, such as EMIB and Foveros.
Chiplets: Intel's packaging technology and the Universal Chiplet High-Speed Interconnect Open Standard (UCIe) will help chiplets produced by different suppliers or with different process technologies to work together more effectively.
Software: Intel's open-source software tools, including OpenVINO and oneAPI, have accelerated product delivery, allowing customers to test solutions before production.
This marks a paradigm shift from system-level chips to system-level packaging, and it is also a manifestation of Intel's efforts to make its foundry services more open.
In addition to reinforcing its foundry fortress with "system-level foundry", Intel also plans to establish a greater decision-making separation between its chip design and manufacturing, aiming to operate the production line like a Fab business, treating orders from internal and external chip companies equally.This decision is known as the "new phase of Intel's IDM 2.0 strategy," and the logic behind it is that Intel wants to decouple its chip design and manufacturing.
Intel's chip design and manufacturing departments have long been highly integrated, which, while increasing flexibility, has also created a problem: the entire design and production process follows an "internal process." In other words, due to differences in the process, chips designed by Intel according to the "internal process" are not easy to find other foundries to manufacture. And other Fabless-designed chips that want to find Intel for manufacturing also need time to adapt to Intel's "internal process," which is also difficult.
The IDM 2.0 transformation proposed by Gelsinger is actually to decouple chip design and chip manufacturing capabilities under the original Intel IDM model, and the ultimate goal is also to enable Intel to achieve better chip design and manufacturing capabilities, while establishing its own chip foundry ecosystem.
The new structure aims to operate Intel's chip foundry business like other third-party wafer foundries, accepting orders from both internal and external chip companies on an equal basis.
Gelsinger understands the crux of Intel's problems. The IDM model that has been proud of for decades is no longer suitable for today's era dominated by TSMC, but completely giving up its own advantages and following the opponent's track is also not conducive to Intel's return to the forefront of the era. Gelsinger hopes to decouple Intel's chip design and chip manufacturing capabilities through the IDM 2.0 transformation, and form a joint force to promote Intel to become a new technological leader.
Intel's confidence and frustration
In addition to strategic transformation, Intel has also made progress in process roadmap and capacity. Intel has formulated a plan to accelerate process development, overthrowing the traditional chip naming method, and formulated a detailed development route to 2025, promoting five process nodes: Intel 7, Intel 4, Intel 3, Intel 20A, and Intel 18A.
In theory, Intel 20A is a process that competes with TSMC's 2nm. Once Intel successfully breaks through the mass production of Intel 20A, it may have the ability to compete with TSMC's 2nm. The more advanced Intel 18A is the layout below 2nm.
It is not difficult to feel that Intel's goal is very clear, trying to form a tripartite situation in the chip foundry industry with TSMC and Samsung, occupying a place in the high-end chip market.
In Intel's third quarter financial report for 2022, it was revealed that it has signed contracts with 7 of the top 10 global semiconductor design manufacturers.The above points are the reasons and confidence behind Intel's bold claim to become the world's second-largest wafer foundry by 2030.
However, before the bold words could be digested, only half a month later, it was reported that Intel's chip foundry service president, Randhir Thakur, would resign in the first quarter of next year.
As a key part of IDM 2.0, Gelsinger has high hopes for IFS and Thakur. In fact, under Thakur's leadership, IFS has indeed won chip customers including Amazon, Qualcomm, and MediaTek. Gelsinger praised him for building a leadership team composed of experienced employees from leading foundries such as TSMC and Samsung, and winning major customers in the mobile and automotive fields.
However, halfway through the venture, Thakur still resigned. The departure of this leader may expose that the internal resistance of Intel may exceed the imagination of the outside world. Or perhaps this will be the key for Gelsinger to further decouple the chip design and chip manufacturing teams.
Samsung Electronics: Surpass TSMC within 10 years
Although both Samsung and Intel are IDM manufacturers, their situations are not quite the same.
Compared with the highly integrated relationship between Intel's chip design and manufacturing departments, Samsung's chip design and manufacturing businesses are relatively independent. For example, many chip products of NVIDIA and Qualcomm are manufactured by Samsung.
Due to the "openness" of Samsung and TSMC in foundry services, fabless manufacturers like NVIDIA can "jump around" relatively freely, choosing foundry manufacturers at will.
Surpass TSMC by 2030Intel plans to surpass Samsung's foundry business by 2030, while Samsung has also declared its goal to surpass TSMC by 2030. In fact, as early as 2019, Samsung set a goal to surpass TSMC within the next ten years. To achieve this goal, Samsung has heavily invested and recruited talent. In addition to continuously increasing its investment in advanced processes, semiconductor equipment and materials, IC substrates, advanced packaging, and all areas related to wafer foundry have become the focus of its aim.
Recently, Samsung has also been very active, not only claiming to expand some non-memory chip outsourcing such as CIS and DDIC, but also expanding traditional and specialty process capacity. Moreover, it has boldly stated that the number of wafer foundry customers will increase to five times that of 2019 by 2027. In addition, it is also advancing step by step in the field of advanced processes.
These actions not only show Samsung's ambitious intentions but also confirm the winning strategy of the foundry industry: capacity, customers, and advanced processes.
Gartner believes that Samsung's actions are obviously well-considered. Most CIS and DDIC products are manufactured at 40nm and above nodes, and their competitive advantages are not prominent. Coupled with the current weakening demand for CIS and DDIC, the overall scale has slowed down. Therefore, whether it is the purchase of EDA, equipment, and materials, or maintenance costs, they are all facing dynamic changes. From the perspective of cost, if the self-produced cost is high, choosing a foundry with good cost control is a good choice.
Samsung is considering outsourcing more mature process chips, in addition to the existing wafer foundry partner UMC, it will also add World Advanced and Powerchip to its foundry chip partners.
In fact, Samsung has many years of outsourcing business in its development process. This strategy has brought it the opportunity to reconfigure resources and factory capacity, achieving more capacity release. Under the capacity allocation, Samsung foundry can undertake more high-interest orders, especially since the mature process equipment has been fully amortized, so the product mix can be more flexible.
As Samsung adjusts its capacity, the news of its intention to expand traditional and specialty processes is also fermenting at the same time.
Among them, the development of specialty processes has become a consensus in the industry. In the current situation where advanced processes are becoming more and more high-end and niche, specialty processes are becoming a new driving force for the wafer foundry industry.
It is understood that there are many players in the global specialty process field, which can be roughly divided into three categories: one is IDMs engaged in analog, MCU, and power semiconductors; the second is wafer foundries mainly focused on specialty processes; and the third is wafer foundries that focus on advanced processes while also taking into account specialty processes.As a latecomer, Samsung has great ambitions. It is reported that Samsung Electronics' semiconductor foundry business plans to increase the number of traditional and specialty processes by more than 10 by 2024. By 2027, Samsung Electronics' capacity for traditional and specialty processes will reach 2.3 times that of 2018.
Advanced processes are advancing step by step
In addition to outsourcing mature processes and focusing on specialty processes, Samsung's expansion and investment in advanced processes are the most eye-catching, aiming to seize the initiative when the next technological point arrives.
As the only two companies in the world that can currently manufacture wafers below 5nm, Samsung's achievements in foundry are not to be underestimated. However, compared to TSMC, Samsung always seems to be one step behind. After Samsung's 7nm mass production, TSMC announced the mass production of 5nm; after Samsung's 5nm mass production, TSMC announced the trial production of 4nm, always unable to keep up with TSMC's pace.
But Samsung sees an opportunity to catch up in more advanced nodes. Samsung's 3nm chips were the first to adopt the GAA process and were mass-produced ahead of TSMC, becoming the world's first foundry to mass-produce 3nm. Building on this success, Samsung Electronics plans to launch the second-generation 3nm process next year and further claims to plan to reach 2nm by 2025 and 1.4nm by 2027.
Regarding this aggressive goal, Isaiah Research believes that Samsung's plan is possible, but the scale of mass production and yield at that time will need continuous attention.
If Samsung is "fighting on both sides" in advanced and specialty processes, then attracting as many customers as possible is the key to "being successful on both sides." Samsung once boldly stated that the number of wafer foundry customers will increase to five times that of 2019 by 2027.
According to Gartner analysis, the business of Samsung's three major US customers more than doubled in 2021. Although there were "changes" in 2022 with Qualcomm and Nvidia transferring orders, the overall "basic situation" is positive. Samsung's vice president of the foundry division, Moon-soo Kang, confirmed in the business call of the first quarter of 2022 that Samsung already has orders for the next five years. He pointed out that these orders are eight times the sales of Samsung's foundry last year.
It is also worth noting that Qualcomm claims that future 3nm and 4nm APs will be manufactured by TSMC, but after entering the GAA process, it may adopt a multi-supplier strategy of placing orders with Samsung and TSMC and other foundries at the same time, which means that TSMC will no longer "monopolize" Qualcomm's advanced process orders, and Samsung may gain more "returning customers" by taking the lead in adopting the GAA advantage of 3nm.
Isaiah Research believes that if Samsung wants to achieve the goal of increasing the customer scale to five times by 2027, it needs to continue expanding production and improving the yield of advanced processes, so as to expand to more potential customers and increase the stickiness of existing customers.In terms of production capacity, Samsung expects that by 2027, its foundry production capacity will increase by 3.3 times compared to 2022. This also means that more factories need to be built. According to foreign media reports, Choi Si-young, President of Samsung Electronics' foundry business division, revealed that the company currently operates 5 factories in South Korea and the United States, and has already determined the locations for more than 10 additional factories.
For Samsung, yield rate has always been a "tiger" to be overcome. It is understood that Samsung's 4nm yield rate has been rising from 35% at the beginning of this year, but it is still unknown how much it has improved now. Compared with TSMC's 4nm yield rate of 70%, and with major customers such as Apple, Qualcomm, and AMD "supporting", this gap still exists. Moreover, Samsung's advanced process customer base is mostly small and medium customers, and how to compete for the favor of major customers from the perspective of production capacity still needs to be worked on.
Gartner also believes that with the availability of relevant software and hardware resources, Samsung needs to overcome the current challenges of the 3nm platform, including yield rate and customers, etc. How to retain new and mature customers in the future 1.4nm platform, and the competitive direction with TSMC and Intel are all variable X factors.
In order to vigorously promote its foundry business, Samsung is advancing on multiple fronts. With the global manufacturing industry returning and leading to the diversification of the supply chain, it will also trigger restructuring in the next few years. Whether it can seize the time window and realize the "decade-old wish" after attacking on all sides still needs to be proven by actions and time.
TSMC: Fearless of Samsung and Intel's Pursuit
On one hand, there is the resignation of Intel's executives and Samsung's production capacity allocation, and on the other hand, there is TSMC's continuous increase in investment.
Currently, TSMC is investing $12 billion to build a 12-inch 5nm process wafer factory in Arizona, USA, which is about to complete the civil construction. It is expected to hold the first machine equipment entry ceremony in December, and recently a large number of American engineers who have been trained in Taiwan, China, have returned to the United States.
On November 21, TSMC founder Zhang Zhongmou confirmed the news of building a 3nm factory in the United States. However, Zhang Zhongmou did not disclose the investment scale of the 3nm wafer factory construction plan in the United States, nor when it will be launched.
But according to industry insiders, the 3nm factory's production capacity will also be 20,000 wafers, and personnel planning is currently underway, with an expected investment scale of $12 billion. This will also be TSMC's third wafer factory in the United States. In addition to the under-construction Arizona wafer factory, TSMC also has a wafer factory in Camas, Washington State, USA, but here only produces 8-inch wafers, mainly for mature processes above 28nm.
Why continue to build advanced process wafer factories in the United States?In 2019, as the US government continued to promote the return of manufacturing to the United States, TSMC announced a plan to invest $12 billion to build a 5nm wafer factory in Arizona. But for TSMC, it is obviously more expensive to manufacture chips in the United States, and this is not a decision based on business costs. Morris Chang once said that the actual cost of manufacturing chips in the United States is 50% higher than in Taiwan. TSMC's decision to build a 5nm wafer factory in the United States was made under the "urging" of the US government. Although the "Chips Act" introduced by the United States has stimulated a lot of semiconductor investment, Morris Chang believes that the amount of subsidies is far lower than the amount needed to boost domestic chip manufacturing. Although the chip production in the United States will increase, the unit cost will increase, and it will be difficult for the United States to compete internationally. So why does TSMC plan to build a 3nm wafer factory after building a 5nm wafer factory in Arizona, the United States? Under the current market trends and trade relations, the overall proportion of US customers in TSMC's revenue is continuing to increase, which is also a major factor in prompting TSMC to build advanced process wafer factories in the United States. According to Digitimes statistics, the United States is TSMC's largest sales market in 2021, with a year-on-year growth of 24% and a revenue share of 64%. Among them, Apple alone accounts for more than 1/4 of TSMC's revenue. At the same time, according to Taiwanese media reports, "Tesla will entrust 4nm and 5nm process products to TSMC." If true, Tesla will enter TSMC's top 7 customer companies, further increasing the share of US companies. In addition, TSMC's construction of advanced process wafer fabs in the United States has also complied with the supply chain security needs of American customers from decentralized sources of supply to a certain extent. According to Bloomberg, Apple plans to purchase chips from a wafer fab under construction in Arizona, USA in the future (the factory will be put into use in 2024) to reduce its dependence on the Asian supply chain. The wafer fab under construction referred to by Apple is generally believed to be TSMC's Arizona wafer fab. Driven by a series of factors, TSMC has been prompted to build another advanced process wafer fab in the United States.On the other hand, due to TSMC's dominant position in the field of chip manufacturing, with the rise in manufacturing costs of its latest 3nm process technology, TSMC will also significantly increase the price of 3nm wafers.
According to the latest exposed TSMC wafer pricing chart, TSMC's 7nm wafer foundry pricing is $10,000, and it has risen to $16,000 for 5nm, an increase of up to 60%. With the rise in TSMC's 3nm manufacturing costs, Digitimes estimates that the wafer foundry pricing will exceed $20,000, a 25% increase compared to 5nm, which means that the next generation of 3nm CPUs and GPUs will be more expensive.
However, the key reasons for this situation are mainly two aspects: on the one hand, as the process technology improves, the requirements for semiconductor equipment and materials become more stringent, directly leading to an increase in manufacturing costs; on the other hand, there are currently only TSMC and Samsung that can provide cutting-edge wafer foundry services, with TSMC alone occupying most of the market share. This near-monopoly situation has also led to the unimpeded surge in the price of each generation of cutting-edge wafer foundry.
The latter is also one of the main factors of the multi-source foundry strategy of current IC design companies.
At present, all major manufacturers are actively deploying more advanced process investments. TSMC President Wei Zhejia has repeatedly stated that TSMC's 3nm will be mass-produced in Taiwan this year, and 2nm will be mass-produced in 2025 while maintaining a leading advantage. However, no mass production schedule for more advanced processes below 2nm has been announced.
TSMC is relatively smooth in the field of advanced processes. It is reported that although the 3nm process has not yet been mass-produced, TSMC's 3nm yield rate has reached 80%. Its largest customer, Apple, has already pre-ordered its M3 chip to use TSMC's 3nm process. There are even reports that TSMC's 2nm risk trial production yield rate has also exceeded 90%, and Apple and Intel, as well as other giant companies, will also be the first batch of customers for TSMC's 2nm.
Recently, according to Shen Rongjin, the deputy head of the administrative region of Taiwan, China, TSMC's 1nm factory will be located in Longtan, starting from Taoyuan Longtan, passing through Xinzhu, Taichung, Tainan, and Kaohsiung. In this way, the entire semiconductor cluster can be fully connected, allowing the western part of Taiwan to have a complete semiconductor technology corridor. It is estimated that the future TSMC 1nm factory will also bring tens of thousands of engineering job opportunities with an annual salary of one million to the local area of Longtan.
Faced with the pursuit of Intel and Samsung, some industry insiders have said that TSMC's advantage has been established, and this advantage is based on top-notch processes. TSMC's financial report for 2021 shows that the shipment of 5nm chips accounted for 20% of its total revenue, and 7nm accounted for 30%. This represents that advanced processes almost account for half of TSMC's revenue, which is a terrifying proportion. This means that TSMC's advantage in advanced processes is not only difficult to narrow the gap with competitors, but may also be further widened.
In conclusion,As advanced processes continue to evolve, TSMC, Samsung, and Intel, the three major chip giants, are set to face a new showdown.
Currently, TSMC's second phase of the 2nm factory expansion plan has been finalized, with construction scheduled to start in the third quarter of this year; Samsung announced in July that it has begun preliminary production of 3nm process chips using the GAA architecture, and the mass production time for the 2nm process is also set for 2025; Intel has previously committed to regaining a leading position in chip manufacturing technology by 2025 and has set the target for mass production of 2nm to 2024.
Intel's rapid catch-up and entry are changing the current "duopoly" competitive landscape of the wafer foundry industry.
However, the market's response to Intel's challenge often requires a longer cycle, and after Intel was left behind by TSMC and Samsung in 10nm and 7nm, regaining customer trust will also take a longer time, so the catch-up process may be a longer one.
Samsung has also frequently fallen into the quagmire of yield in advanced processes and urgently needs improvement.
Industry experts emphasize that TSMC has not become the absolute winner in the foundry market, as most wafer foundry manufacturers have completely said goodbye to the competition of advanced processes, leaving many customers with no choice but to choose between TSMC, Samsung, and Intel. TSMC's production capacity alone is difficult to maintain the huge market for advanced processes. Therefore, even if Samsung and Intel's chips will face the risk of a "Waterloo" in performance, there will still be a large number of manufacturers willing to "try the crab" driven by factors such as production capacity and price.
In the future, the competition for advanced process chips will mainly take place between TSMC, Samsung, and Intel, and the tug-of-war among the three giants in foundry will also become the driving force to continue to advance Moore's Law, promoting the arrival of the next "bend."
Every driver knows that a bend represents too many possibilities. When an era begins to turn, the leader may fall behind, and the laggard may surpass.
Post Comment