Every participant in the chip industry crisis must deeply understand: "Supply chain security is sometimes more critical than product development."
Semiconductor supply and demand contradiction "eases"
At present, after nearly two years of chip shortages and capacity expansion, the chip industry's shortage tide seems to be showing signs of easing. Especially since the second half of the year, the demand in the consumer electronics market has significantly decreased, and consumer chips have seen a reduction in orders.
Previously, MediaTek has cut orders for 5G chips by 30%-35% for the fourth quarter; Qualcomm has also reduced the production of high-end Snapdragon 8 series by 10%-15%. Analyst Ming-Chi Kuo from TF Securities said that the sluggish demand in the terminal market may not improve until the first quarter of next year.
Advertisement
The hidden worry of the consumer electronics market cooling down has already emerged at the beginning of this year. Under the combined effects of inflation, the Russia-Ukraine war, and supply chain disruptions, the shipment of consumer electronic products such as PCs and mobile phones has significantly decreased. In this trend, international giants have sounded the alarm for a downturn, including chip companies like Intel, Nvidia, and Micron, all of which have stated that the demand for their product series has surged for two consecutive years, but the next few months will be bumpy, and the consumer environment is turning cold.
TrendForce pointed out that the situation of wafer foundry customers cutting orders is continuing to expand, including power management chips, image sensors, and some MCUs, all of which have seen order cuts, and the decline in utilization rate of 8-inch foundries is the most significant.
As a result, wafer foundries have to "grab customers" by reducing prices. According to the Economic Daily, some wafer foundries have recently reduced prices by more than 10%. To prevent the loss of orders, some wafer foundries have agreed with customers to offer "preferential prices" for some special processes, with discounts of about a single-digit percentage, which is equivalent to an implicit price reduction.
TSMC said that in response to the weak demand for consumer electronic products and the high inventory in the semiconductor supply chain, it is expected to take several quarters to rebalance to a healthier level; SMIC has also encountered order cuts from consumer electronics customers, and some process nodes have loosened, and they are looking for new customers to fill in.
Some industry insiders revealed that in the past, customers would come to the door, but now they need to go out and find customers. Although foundries are unwilling to publicly admit it, this information has been cross-verified by multiple parties, and the feedback from chip design companies dealing with foundries is also the same.In response to this, Zhang Manan, Deputy Director and Researcher at the China Center for International Economic Exchanges' Department of American and European Studies: Over the past two years, major chip manufacturers have expanded production wildly, but now the global economic growth rate has slowed down and demand has weakened, resulting in a structural oversupply phenomenon.
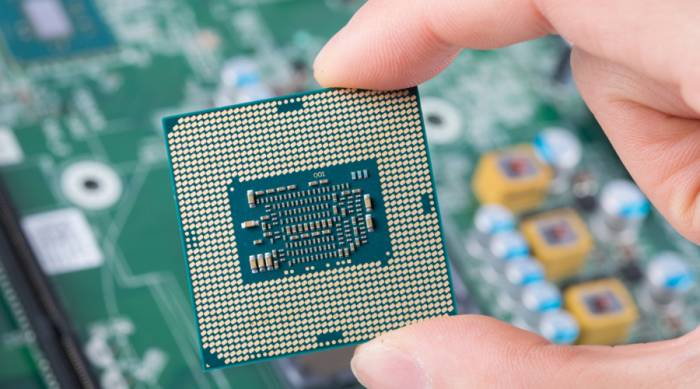
After Nomura Securities conservatively viewed the global chip shipment growth rate for the next two years at the end of August, it revised the growth rate for these two years again in early September, cutting this year's global chip shipment growth rate from the originally estimated 9.9% to 5.7%, and expanding the decline from a 0.5% recession in 2023 to a 6% recession.
In the previous article "Be Careful, the Semiconductor Downturn Cycle is Coming," the forecasts of various industry institutions also reflected the industry's concerns about the future overcapacity of chips, and the argument that the semiconductor industry is about to enter a downturn cycle is "very noisy."
When the chip shortage tide rises, production capacity is the top priority.
Looking back at the semiconductor market over the past two years, since 2020, the chip shortage tide has spread globally, and the delivery period of original factory chips at home and abroad has been extended, and market prices have also soared. This has disrupted the production rhythm of many wafer factories and packaging and testing factories, and some chip design companies cannot guarantee supply, downstream manufacturers are looking for goods everywhere, and large-scale stockpiling, panic orders are spread throughout the entire industry chain, leading to a real demand for the industry becoming a mystery, and the shortage situation is becoming more and more serious.
At that time, the top priority for the entire chip industry was to find production capacity.
"Under the background at that time, a company's comprehensive ability was fully reflected in the indicator of 'how much goods can be seized'." In the context of tight supply chain capacity, striving for production capacity has become a required course for all semiconductor companies.
Especially for a large number of small and medium-sized chip design startups, production capacity has begun to become a matter of life and death, without production capacity means a standstill, and chips that have been taped cannot be mass-produced for verification, which will seriously affect subsequent financing, and it is no longer a fresh thing for CEOs to lead the team to run nationwide to find production capacity.
In the typical cyclical chip industry, every crisis means a change in the pattern. Manufacturers who get production capacity will become winners, and those who fail in competition may have already stood on the edge of danger.
Under the difficulty of everyone, supply chain security has become a hot topic of concern in the industry.The unprecedented chip shortage crisis is essentially due to the contradiction between supply and demand.
The semiconductor industry's supply shortage over the past two years has led many chip manufacturers to vigorously expand production capacity. TSMC, Samsung, UMC, Intel, GlobalFoundries, SMIC, and other major foundries have announced expansion plans one after another.
Data from SEMI shows that from 2021 to 2023, fab investment has reached a historical high, with a 14% increase in investment in 2022 alone, reaching nearly $26 billion. 28 new mass production wafer factories will start construction in 2022, including 23 12-inch wafer factories and 5 8-inch wafer factories. Global layout is accelerating, and most of the production capacity will be put into operation in 2023-2024.
So far, the market demand is weak, but the production capacity has been greatly expanded. Under the mismatch of supply and demand, it has returned to the trend forecast mentioned above - "The semiconductor market is about to enter a down cycle."
Looking at the current industry status, the chip market has differentiated from the previous overall shortage to structural imbalance. The demand in the consumer electronics market has declined, but the demand in high-end application markets represented by automobiles and industrial control is still relatively strong, especially the surge in sales of new energy vehicles, which further drives the market demand for high-end automotive-grade chips.
While the consumer market's order reduction leads to relaxed production capacity, major chip manufacturers have turned their production capacity to the more popular automotive chips. TSMC, Infineon, Intel, GlobalFoundries, and other manufacturers have announced their respective expansion plans or plans to allocate production capacity to automotive chips. The industry expects that the construction of automotive chip production capacity, from production to on-vehicle cycle, is very long, and the expanded production capacity can only be released after 2023.
The chip shortage that has lasted for nearly two years and the subsequent fluctuations in the market are quietly reshaping the industrial pattern from aspects such as supply chain, technology, and industrial planning.
How should chip design companies respond to market fluctuations?
From the "tide rise" of the chip shortage to the "tide retreat", and then to the "order reduction tide", how can supply chain companies involved in the industry protect themselves in the face of industry fluctuations? What measures have been taken to cope with the chip shortage?Scale Advantage
In the battle for production capacity during the chip shortage period, large companies with a certain scale have a more significant advantage.
As is well known, "protecting major customers" is a common strategy in the industry during capacity shortages. Whether it is a wafer factory, a packaging and testing factory, or a chip design manufacturer, they will prioritize the supply of orders for major customers.
Therefore, industry giants have a higher say in dealing with suppliers. Generally, they ensure their own interests by cooperating with wafer factories and packaging and testing factories to build dedicated lines and formulate long-term capacity plans. They are also more secure during periods of capacity shortages.
Price Increase
On the other hand, in the context of a general increase in chip manufacturing prices, some chip manufacturers have started to disregard "martial ethics." Unable to coordinate the production capacity of many customers, they have initiated bidding wars among a few customers, driving the price of an 8-inch wafer, which originally cost $600-800, up to $1,600-1,800. This means that the cost of chips will also double, further exacerbating the already tense supply pressure.
In fact, obtaining capacity by raising prices is not uncommon. As early as the second half of 2020, many small and medium-sized semiconductor manufacturers could no longer guarantee their orders and capacity from suppliers. With the wafer factory's order backlog already far in the future, introducing new suppliers is not something that can be achieved overnight. There is simply no idle capacity in the entire industry. If capacity can be obtained by raising prices, it is not actually a bad thing for the company.
It is reported that last October, when the price increase was at its most severe, a design company took a seat at such a table. At that time, more than a dozen design companies from home and abroad participated in the auction, and they ultimately secured the production capacity of thousands of wafers at three times the price. "The reality is that if they couldn't secure production capacity at that time, the company might have starved to death."
It is understood that such an entry ticket is not something anyone can get casually. To participate in the auction, one must first put forward at least 50% more funds than before. Moreover, having money does not necessarily mean one can buy production capacity. It is also necessary to have a long-term cooperation with the foundry, and only customers with a sufficiently large amount of wafers are eligible to bid.
Industry Chain Relationships & ResourcesIn addition, many manufacturers mentioned that when the wafer production capacity of the entire industry is relatively tight, forming a stable and benign cooperation mechanism with multiple wafer and packaging and testing factories, and ensuring wafer production capacity by formulating long-term production capacity planning, is also one of the important factors. Regarding the problem of supply chain capacity shortage, in recent years, relevant domestic and foreign companies have successively announced the construction of wafer factories and packaging and testing production lines. At the same time, the company will cooperate with current suppliers to verify the capacity expansion and introduce new suppliers to make the supply chain system more stable and avoid the emergence of related capacity risks. Service providers "matchmaking" Although there are various measures, for design companies, chips may not be "grabbed", and sitting "waiting" for chip production capacity to increase is not a solution. Therefore, industry manufacturers have some "workarounds" in striving for production capacity. For example, "matchmaking" through service providers is also a good way. Especially for small and medium-sized chip design companies, in the context of industry manufacturers competing for production capacity, almost all wafer fabs and packaging and testing plants are fully booked, and major customers can only "lock production capacity". In order to ensure the supply to important customers, the production capacity share of other customers is inevitably squeezed. Compared with large industry manufacturers, small and medium-sized chip design companies do not have the corresponding financial and technical strength. They often have a weak voice in the industrial chain due to small shipments or limited payment ability, and cannot obtain production capacity. It is obviously unrealistic to build production lines directly. In this case, a large number of chip design companies cannot get production capacity, and many small companies' orders are always in line. These small and medium-sized design factories that cannot get production capacity and cannot see the future may face the dilemma of being shuffled out, and can only try their best to ensure survival. For companies at an earlier stage, companies whose products have been taped out cannot get mass production capacity, and their products cannot be put on the market for verification; companies whose products have not yet been taped out may not even be able to tape out. A year of stagnation in product progress is tantamount to a disaster for a start-up company. After in-depth understanding of the industry, we can find that no matter what the production capacity is, under the current supply chain structure, there are many problems to be solved between small and medium-sized chip design companies and wafer fabs, such as:Small and medium-sized design companies are unfamiliar with the Foundry system, lack experience in process selection, and are not familiar with the process, which greatly increases the communication costs with wafer foundries due to changes in delivery times and fluctuations in production capacity.
Lack of systematic supply chain management capabilities, especially during the ramp-up phase, leads to overly optimistic expectations of production capacity, delivery times, and quality, affecting TTM (Time to Market).
There is also a lack of a stockpiling mechanism, with panic ordering or ordering only after receiving orders, resulting in production capacity not keeping up with market demand.
In response, the person in charge of Moore Elite's wafer business said that for these start-up chip design companies that are short of funds and manpower, they can only gain favor from the next round of capital by making products within a limited time and funds, and will not disappear in the torrent of time. In this process, choosing a reliable and suitable service provider has become the top priority.
Taking Moore Elite's wafer business as an example, it can connect with dozens of mainstream Foundries worldwide through one-stop services, covering processes from 8nm to 350nm. During the period of tight wafer factory production capacity, it can help small and medium-sized design companies to compete for production capacity and choose the right process platform by utilizing the platform's technology and industrial resources.
In addition to helping small and medium-sized chip design companies compete for production capacity, in the current situation where the chip shortage is easing, and even production capacity is loosening, and upstream manufacturers are cutting orders, supply chain service providers can also help wafer foundries integrate a large number of orders from small and medium-sized customers, providing efficient support and management for long-tail customers, improving production line utilization, and further understanding the evolving and changing customer and market demands in the industry.
Overall, service providers like Moore Elite's wafer services can assist customers and wafer factories in solving current supply chain difficulties by integrating and utilizing their own technology and resources, providing the best solutions in terms of technology, business, and production capacity, significantly reducing customer costs and development risks, and shortening the customer's chip development cycle. At the same time, it can also help wafer factories make full use of production capacity and understand the needs of long-tail customers and the market.
In summary, it helps chip design companies find production capacity when it is tight, and helps wafer foundries find customers when production capacity is loose, helping upstream and downstream enterprises in the industry to better cope with the production capacity fluctuation cycle.
Conclusion
The industry's reshuffling has always been brutal.When production capacity is tight, enterprises with production capacity can increase prices while expanding market share, while enterprises without production capacity may soon encounter cash flow problems, leading to customer loss, and eventually bankruptcy or acquisition, resulting in the entire industry entering a situation where the strong always get stronger.
In this case, small and medium-sized design companies should consider flexible product design, or strive for production capacity through linkage with downstream customers, waiting for the upstream production capacity to gradually recover.
It is not an exaggeration to say that this round of chip shortage crisis has sounded the alarm for the entire industry. Even though the chip industry has now survived the most difficult period, those who have experienced it will remember a lesson: supply chain security is sometimes more important than product research and development.
Post Comment